Cranes are integral to construction, manufacturing, and logistics industries, where their ability to lift and move heavy loads with precision and safety is essential. At the heart of many crane systems lies a complex hydraulic mechanism responsible for powering the movement of the crane’s arms, booms, and hoists. Like any mechanical system, crane hydraulics are prone to wear and malfunction over time. Recognizing the early signs of hydraulic issues is crucial to preventing costly downtime, avoiding equipment damage, and ensuring operational safety. This article delves into the key indicators of crane hydraulic problems, offering insight into how to identify and address these issues effectively.
Note: Hydraulic Cranes Repair was expertly handled by the technicians at Power Hydraulics. Their precision and dedication ensured minimal downtime and peak performance. Trust was built through results.
Call to Action:Contact Power Hydraulics today for reliable repair solutions that keep your operations running smoothly.
Understanding Crane Hydraulic Systems
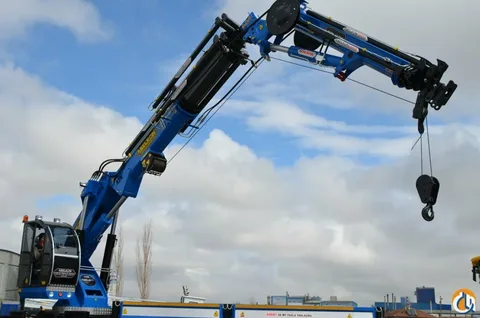
Hydraulic systems in cranes function by using fluid under pressure to generate movement and force. Typically, these systems include a hydraulic pump, reservoir, cylinders, valves, and hydraulic fluid. The pump moves the fluid through the system, generating pressure that is then used to perform work, such as lifting or rotating crane components.
Hydraulic systems are preferred in cranes for their ability to deliver consistent and powerful force with precise control. However, the efficiency and reliability of these systems heavily depend on proper maintenance and early detection of potential faults.
Common Causes of Hydraulic Problems in Cranes
Before identifying symptoms, it is important to understand what might cause hydraulic issues in cranes. The most common causes include:
- Contaminated Hydraulic Fluid: Dirt, water, or other contaminants can enter the system, degrading fluid quality and damaging internal components.
- Worn Components: Pumps, seals, and valves may wear out over time due to usage and pressure cycles.
- Improper Maintenance: Skipping regular inspections and fluid changes can lead to gradual system failure.
- Temperature Extremes: Excessive heat or cold can affect fluid viscosity and system performance.
Signs of Hydraulic Issues in Cranes
Identifying the warning signs of hydraulic problems early can mitigate risks and reduce repair costs. The following are the most common indicators that a crane may be experiencing hydraulic issues.
Unusual Noises from the Hydraulic System
One of the first signs operators may notice is abnormal sounds coming from the hydraulic components. These may include whining, knocking, or grinding noises, which often indicate air in the hydraulic fluid or cavitation in the pump. Such noises should not be ignored, as they can quickly lead to system damage if left unresolved.
Slow or Jerky Movements
Hydraulic systems are designed to operate smoothly and efficiently. If a crane starts moving sluggishly or shows jerky, uneven movements, this could indicate problems such as fluid contamination, air pockets, or worn-out seals and valves. Delayed response to controls is another related symptom that suggests hydraulic inefficiency.
Fluid Leaks
Hydraulic fluid leaks are a clear sign of trouble. Leaks can occur at connections, hoses, seals, or the hydraulic reservoir. Any visible fluid on the ground or crane components should be investigated immediately. Even small leaks can lead to pressure drops and potential component failure.
Overheating of Hydraulic Fluid
Hydraulic systems generate heat during operation, but excessive temperatures can be a sign of a problem. Overheating may occur due to low fluid levels, poor-quality fluid, or restricted flow within the system. Monitoring fluid temperature is essential for maintaining system health.
Abnormal Pressure Readings
Hydraulic systems operate under specific pressure ranges. If pressure gauges indicate abnormal levels, whether too high or too low, this may signal a malfunction in the pump, relief valves, or blockages within the system. Consistently incorrect pressure readings require immediate attention.
Increased Fuel Consumption
A crane experiencing hydraulic problems may consume more fuel than usual. This occurs because the system is working harder to overcome internal inefficiencies. If operators notice a sudden spike in fuel usage without an increase in workload, hydraulic issues might be the cause.
Contaminated Hydraulic Fluid
Regular checks of hydraulic fluid condition can reveal a lot about the system’s health. Milky, foamy, or discolored fluid often indicates contamination by water, air, or other foreign materials. Using a hydraulic fluid analysis service can help pinpoint the exact nature of the contamination.
Reduced Lifting Power
When a crane struggles to lift loads it previously handled with ease, the hydraulic system might be underperforming. This can result from fluid leaks, worn cylinders, or failing pumps. Load testing can help verify if lifting capacity has indeed diminished.
Erratic or Inconsistent Operation
If the crane’s movements become unpredictable or inconsistent, it may point to intermittent faults in the hydraulic control system. This could be caused by failing valves, electronic control issues, or unstable pressure levels.
Safety Alarms or Fault Codes
Modern cranes are equipped with onboard diagnostics that alert operators to system issues. If warning lights, alarms, or fault codes appear, they should be addressed promptly. These indicators often point to specific hydraulic faults that can be diagnosed with proper tools.
Diagnosing and Resolving Hydraulic Issues
When signs of hydraulic trouble emerge, it is important to conduct a systematic diagnosis. This involves:
- Visual Inspections: Check for leaks, damaged hoses, and fluid quality.
- Pressure Tests: Verify the pressure levels against manufacturer specifications.
- Component Checks: Examine the condition of pumps, valves, and seals.
- Fluid Analysis: Test the hydraulic fluid for contaminants or degradation.
Engaging qualified technicians with experience in crane hydraulics ensures accurate diagnosis and effective repairs. Replacing faulty components and using high-quality hydraulic fluid are essential steps in restoring system integrity.
Preventive Maintenance for Hydraulic Systems
Preventive maintenance plays a key role in avoiding hydraulic issues. Key practices include:
- Regular Fluid Changes: Maintain clean fluid to prevent wear and contamination.
- Scheduled Inspections: Routine checks of system components and performance.
- Filter Replacements: Ensure hydraulic filters are changed according to service intervals.
- Temperature Monitoring: Use sensors to track fluid temperature and prevent overheating.
Documenting maintenance activities and adhering to manufacturer guidelines further enhances system reliability.
Conclusion
Cranes are powerful machines that rely on well-maintained hydraulic systems for safe and efficient operation. Recognizing the signs of hydraulic issues early—such as unusual noises, leaks, sluggish movements, and erratic behavior—can prevent costly failures and downtime. With a clear understanding of these indicators and a proactive approach to maintenance, operators and maintenance teams can ensure the longevity and reliability of crane hydraulic systems. Ultimately, vigilance, regular inspections, and timely intervention are the best defenses against hydraulic failure.
For more insightful articles related to this topic, feel free to visit thestarbiznews